We made the best television in the world
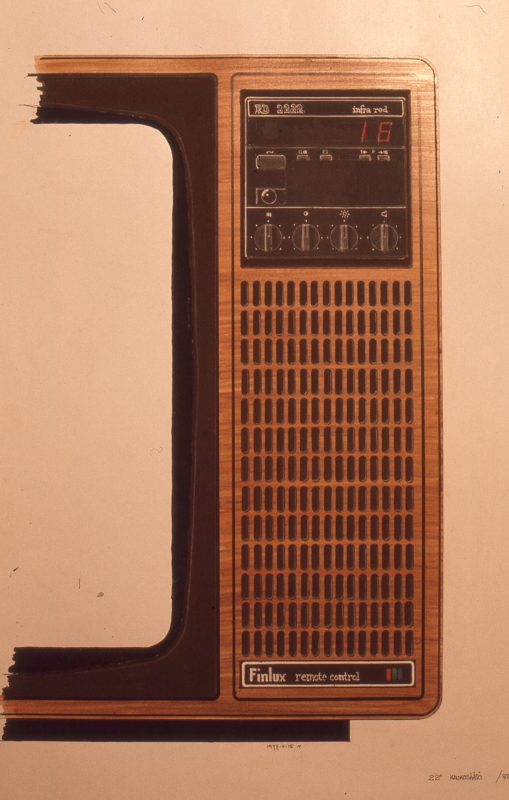
Using wood in the TV mask meant repeated mechanical work in each mask, and that was expensive. A plastic mask would eliminate those costs, but would introduce expensive tooling costs. They were covered by a higher production volume. But how did competitors make a TV box with a plastic mask? To find out, a spy mission was made to the German television casing industry. The designer said he was a designer for Salon Radiolaatikko Oy and an interpreter for Seppo Halminen at an industry trade fair in Germany. In Germany, suppliers to the carpentry industry generously took us to see how their materials are used in production by the cabinet factories. We saw fancy and complicated ways of making things and decided we wouldn’t use anything so fancy and expensive.
In our technique, the plastic parts were attached to the wooden frame with a rivet gun, saving a lot of labour time and expensive metal parts. The TV buyer will not peek inside the TV. The Finlux OBC series (OBC = Optimum Brightness Control) was intended to be a “people’s car”, a TV suitable for every home, and it should be easy to use even for older people. Most of our competitors made TVs that were difficult and complicated to install channels on. It was agreed that the principles of the control unit would be determined by a person with the electronic skills of a grandmother. A designer, that is. A designer wrote a text describing the installation of the channels, and Heikki Tupala designed the control unit that did the trick. Later, competitors’ devices started to work just as easily.
The plastic mask helped to speed up the assembly of the TV. The control unit locked by pushing without screwing. The new technology eliminated parts of the “engine”, making its construction lighter and cheaper. Finlux OBC was a success that made us a productive member of the Lohja family. While the collection was supposed to take three years to produce, it took almost five.
